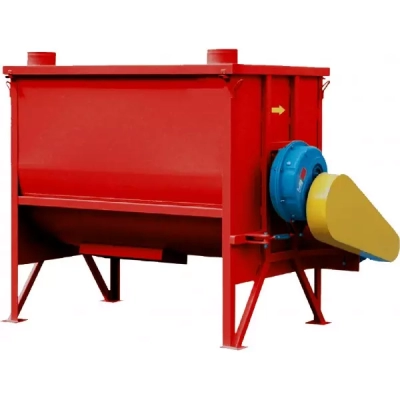
Przekładnie kątowe znajdują kolejne zastosowania w mieszadłach, które stosuje się powszechnie w rolnictwie, przemyśle chemicznym, papierniczym, farmaceutycznym, spożywczym i w oczyszczalniach ścieków. Układ napędowy, czyli motoreduktor plus przekładnia kątowa znajduje się na górze zbiornika, w którym ma zachodzić określony proces technologiczny. Napędza on pionowy wał o określonej długości, na którego końcu umieszczono łopatki mieszadła.
Praca mieszadła odznacza się pewną specyfiką, która stawia przed konstruktorem określone wyzwania:
- zwrócenie wału wyjściowego przekładni ku dołowi stawia wyższe wymagania uszczelnieniu wału.
- długi wał mieszadła pracującego w gęstej cieczy wywołuje znaczne momenty zginające wał wyjściowy przekładni i zauważalne strzałki ugięcia
Mówiąc uszczelnieniach wałów, należy podkreślić wagę jej smarowania, oraz problemów, jakie mogą wystąpić w tym temacie. W istocie smarowanie oznacza oddzielenie współpracujących elementów warstwą filmu olejowego, czyli cienką warstwą oleju, która nie dopuszcza do bezpośredniego zetknięcia się w ruchu metalu z drugim metalem. Rozróżniamy różne typy smarowania, ale w przypadku większości przekładni (do 15m/s prędkości obwodowej kół) mamy do czynienia ze smarowaniem zanurzeniowym. Zbyt małe zanurzenie oznacza niedostateczne smarowanie, a nadmierne zanurzenie w oleju generuje znaczne opory hydrodynamiczne i idące za tym straty mocy. Oprócz smarowania przed środkiem smarnym stawia się jeszcze wymagania w postaci chłodzenia i tego, żeby zabezpieczył mechanizmy przed korozją. Jeżeli idzie o chłodzenie, to na daną wielkość mocy przenoszonej musi przypadać określona minimalna objętość oleju i przyjmuje się ją w granicach 0,3 do 0,8 litra na 1kW. Gdy pojawi się kłopot z zapewnieniem właściwego smarowania, stosuje się rozwiązania wspomagające takie jak na przykład dodatkowa kadź olejowa. Oznacza to dodatkowy otwarty zbiornik wewnątrz korpusu, do którego olej dostaje się w wyniku jego rozbryzgiwania w czasie pracy przekładni. W wyniku rozbryzgiwania tym samym olejem smaruje się łożyska, a jedynie w przypadku mało obciążonych przekładni stosuje się smarowanie smarem stałym i zwykle ma to miejsce w przekładniach otwartych. W niektórych przekładniach stożkowych stosuje się dodatkowe wspomaganie smarowania łożysk w postaci dodatkowej tarczy na wałku wejściowym wraz z kanałem doprowadzającym, którym olej dostaje się w żądane miejsce. Dodatkowe elementy przekładni związane z ich smarowaniem to wskaźniki poziomu, korki spustowe i odpowietrzniki, które służą niekontrolowanemu wzrostowi ciśnienia wewnątrz korpusu podczas zmian temperatury zewnętrznej, a może to grozić wyciekami oleju.
Jeżeli mowa o wyciekach oleju to należy wspomnieć o uszczelnieniach wałów przekładni, tak aby olej nie wydostał się na zewnątrz. Przeważnie stosuje się pierścienie gumowe uszczelniające w wersjach z wkładką usztywniającą lub w zewnętrznej obudowie metalowej i stanowi to rodzaj uszczelnienia kontaktowego, czyli takiego gdzie stykają się elementy stałe i ruchome. Przy mniejszych prędkościach obwodowych wału bardzo rzadko stosuje się pierścienie filcowe uszczelniające lub uszczelnienia bezkontaktowe, a to drugie rozwiązanie mieści w sobie kilka grup takich jak na przykład uszczelnienia rowkowe, labiryntowe i odrzutnikowe. Działanie uszczelnienia rowkowego opiera się na działaniu szczeliny między boczną pokrywą a powierzchnią wału, której niewielki wymiar skutecznie zabezpiecza przed wypływem oleju. W wielu przypadkach na powierzchni pokrywki lub pokrywki i wału toczy się wąskie rowki, w których może się zmieścić część oleju, która jednak wydostanie się przez niewielką szczelinę. Uszczelnienie labiryntowe działa na zasadzie, widocznego w przekroju, zmieniającego kierunek kanału, który tworzą pokrywa boczna oraz pierścień labiryntowy osadzony na wale. Uszczelnienie odrzutnikowe wykorzystuje siłę odśrodkową działającą na krople oleju osadzające się na odrzutniku - rowku lub wystającym elemencie na wale w miejscu, gdzie wychodzi z korpusu.
Poza uszczelnieniami wałów należy wspomnieć o pozostałych uszczelnieniach występujących w przekładniach, a znajdują się one pomiędzy elementami korpusu oraz między korpusem i pokrywami bocznymi. Tutaj stosuje się zazwyczaj pasty uszczelniające.
To, co napisano powyżej wygląda pięknie w przypadku gdy wał wejściowy lub wyjściowy położony jest poziomo. Jeżeli wał wyjściowy przekładni kątowej do mieszadła umieszczony jest pionowo w dół, to część oleju, nawet przy bardzo sprawnym uszczelnieniu, może wydostawać się przez pierścień uszczelniający w dół i na zewnątrz. A jeżeli olej wycieka z przekładni to raz, że jest go coraz mniej a dwa, że w pewnej chwili zacznie się mieszać z płynem, które mieszadło miesza i zamiast mieszać, to co trzeba, to jeszcze dodatkowo miesza olej, którego w mieszanym płynie nie chcemy.
Aby temu zaradzić, stosuje się tak zwaną komorę osuszającą oddzielającą przestrzeń wewnątrz korpusu przekładni od przestrzeni wokół wałka w rejonie dolnego łożyska i wokół niego. W ten sposób powstają niejako dwie przestrzenie oddzielone uszczelnieniem labiryntowym. W miejscu, gdzie komora osuszająca kontaktuje się z piastą koła biernego na wałku wyjściowym. Dla pewności komorę wyposaża się, chociaż nie zawsze, w przewód kontrolny, dzięki któremu można sprawdzić ewentualny wyciek oleju. Ubocznym efektem tego rozwiązania byłby brak smarowania łożyska, ale tutaj stosuje się dodatkowe jego smarowanie przy pomocy smaru stałego napełnianego na etapie produkcji.
Kolejne rozwiązanie w temacie uszczelnienia wału wyjściowego nosi nazwę Drywell, które to rozwiązanie zawiera dodatkowy odrzutnik zamontowany poniżej dolnego pierścienia uszczelniającego. Jak wiadomo, nic nie jest wieczne i taki simmering pewnego dnia zacznie w małych ilościach przepuszczać olej czy tego chcemy, czy nie. Dodatkowy odrzutnik działa w sytuacji gdy jakakolwiek ilość oleju wydostanie się przez pierścień uszczelniający i transportuje go do komory zbierającej - dodatkowego awaryjnego zbiornika w kołnierzu otaczającym wał. Gdy tam zbierze się określona objętość środka smarnego, to jest to sygnalizowane dzięki czujnikowi, który został w komorze zainstalowany.
Jeżeli chodzi o sprawę większych momentów zginających wał z uwagi na długi wał mieszadła, to i tutaj znaleziono skuteczne rozwiązanie o nazwie EBD (Extended Bearing Distance). Wyobraźmy sobie, że większe momenty zginające wywołują wyższe reakcje poprzeczne w łożyskach i w tym miejscu zaczyna się prawdziwy problem, bo to obniża ich trwałość. Rozwiązanie EBD wykorzystuje najprostsze reguły mechaniki, ponieważ łożyska ustawia się w większej odległości od siebie niż dotychnczas i niż by to wynikało z uwarunkowań konstrukcyjnych. Proste i skuteczne, ponieważ większy rozstaw łożysk przy danym momencie zginającym wał automatycznie oznacza niższe reakcje poprzeczne - zasad mechaniki oszukać nie można, ale należy je wykorzystywać.