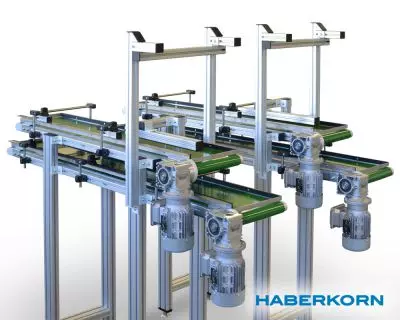
Przekładnie ślimakowe to podzespoły, od których wymagamy niezawodności i dlatego istotne znaczenie odgrywa położenie ślimaka względem ślimacznicy, a mówiąc dokładnie położenie wału ślimacznicy wzdłuż jej osi. Dokładność montażu decyduje o cichobieżności pracy i trwałości przekładni i na etapie produkcji elementów przekładni, korpusu i pokryw łożyska mogą powstać drobne niedokładności wymiarów. Regulacja odbywa się to poprzez dobór odpowiedniej liczby podkładek pod pokrywkami łożysk wału wyjściowego - aby przesunąć wał ślimacznicy o odległość na przykład grubości podkładki, to wymontowuje się jedną z nich i zakłada się pod przeciwną pokrywkę. Druga metoda to zamiana dwóch podkładek różnej grubości pod pokrywkami stronami.
Klasyczne rozwiązanie wału ślimacznicy to jeden czop zwrócony w jedną ze stron, jednak w zastosowaniach przemysłowych często spotykamy drążone wały wyjściowe. Jeden z plusów tego typu rozwiązania to uniwersalność dla wielu aplikacji, ponieważ istnieje możliwość bezpośredniego połączenia z wałem wejściowym odbiornika mocy poprzez połączenie wpustowe.
Druga alternatywa w tym temacie to wał wyjściowy pośredniczący z drążonym wałem wyjściowym i również w tym przypadku dodatkowy element łączy się poprzez połączenie wpustowe. Żeby było jeszcze ciekawiej, to pośredniczący wał wyjściowy może wystąpić w 2 wersjach: pojedynczej i podwójnej. Wał pojedynczy spełnia swoje zadanie w większości przypadków, ale czasem istnieje potrzeba wyprowadzenia napędu na obie strony po to, aby dostarczać moc jednocześnie do 2 odbiorników mocy, ale czasami niezbędne jest okresowe napędzanie maszyny po lewej lub po prawej stronie przekładni.
Po stronie wału wejściowego występuje podobna historia: możemy spotkać klasyczny czop wejściowy albo drążony wał wyjściowy. Pierwszy przypadek to przekładnia ślimakowana, której czopie wejściowym osadza się na przykład sprzęgło i napędza się ją dowolnym silnikiem. Drążony wał wejściowy występuje w motoreduktorach i sprzęga się bezpośrednio z wałem wyjściowym silnika. Można łatwo zauważyć, gdy towarzyszy temu korpus ukształtowany w formie kołnierza pod silnik, także w wykonaniu kołnierzowym.
Łożyskowanie wału wejściowego realizuje się zwykle z jednym łożyskiem stałym i drugim pływającym, przy czym to pierwsze przypada od strony czopa wejściowego i składa się z zespołu dwóch łożysk stożkowych w układzie x i to ten węzeł przejmuje siły wzdłużne i poprzeczne. Przeciwna podpora wykorzystuje łożysko kulkowe zwykłe i ono przenosi tylko siły poprzeczne. Inne rozwiązanie łożyskowania wału wejściowego to oparcie go na dwóch łożyskach stożkowych w układzie x.
Łożyskowanie wału ślimacznicy rozwiązuje się w podobny sposób, czyli dwa łożyska stożkowe w układzie x i we wszystkich przypadkach luz w łożyskach stożkowych kasuje się, stosując odpowiedniej grubości podkładki pod pokrywki łożysk.
Cała przekładnia mieści się w korpusie, który przeważnie jest odlewem z żeliwa, a tylko do korpusów o mniejszych wymiarach używa się stopów aluminium.
Ponieważ przekładnia tego typu zwykle posiada znaczne przełożenie, to przez to generuje duży moment wyjściowy, a duży moment wyjściowy prowadzi do dużych sił obciążających śruby mocujące korpus do podłoża lub ramy. Do przeniesienia ogromnych sił byłyby potrzebne śruby o ogromnej średnicy (nawet te o najwyższej klasie własności mechanicznych), a to komplikuje konstrukcję korpusu. Szczególnej wagi problem nabiera gdy rozstaw śrub jest niewielki, bo jak wiadomo, moment wyjściowy generuje reakcje, a moment równa się siła razy ramię. Aby zminimalizować siły, w śrubach stosuje się tak zwane ramię reakcyjne, które jest właściwie dźwignią mocowaną do korpusu (do kołnierza wokół wałka wyjściowego) w taki sposób, aby przejąć część reakcji pochodzącej od momentu wyjściowego. Drugi koniec ramienia reakcyjnego o odpowiedniej długości mocuje się do ramy - punktu który przejmuje część sił.
Przekładnie ślimakowe znajdują zastosowanie w przenośnikach, gdzie wymagana jest zwartość konstrukcji, mała prędkość obrotowa i duży moment wyjściowy i można je spotkać tam, gdzie wymagana jest duża wydajność przenośnika i wysokość podnoszenia przy małej prędkości liniowej taśmy.